
There are many constitutive equations describing the shear-strain relationship in literature which have had some degree of success for different situations. However, as sediment concentrations increase, they begin to affect the fluid properties, which alter the stress-strain relationship. This assumption appropriate for most fluids, including sediment laden fluids with volumetric concentrations up to 30%.
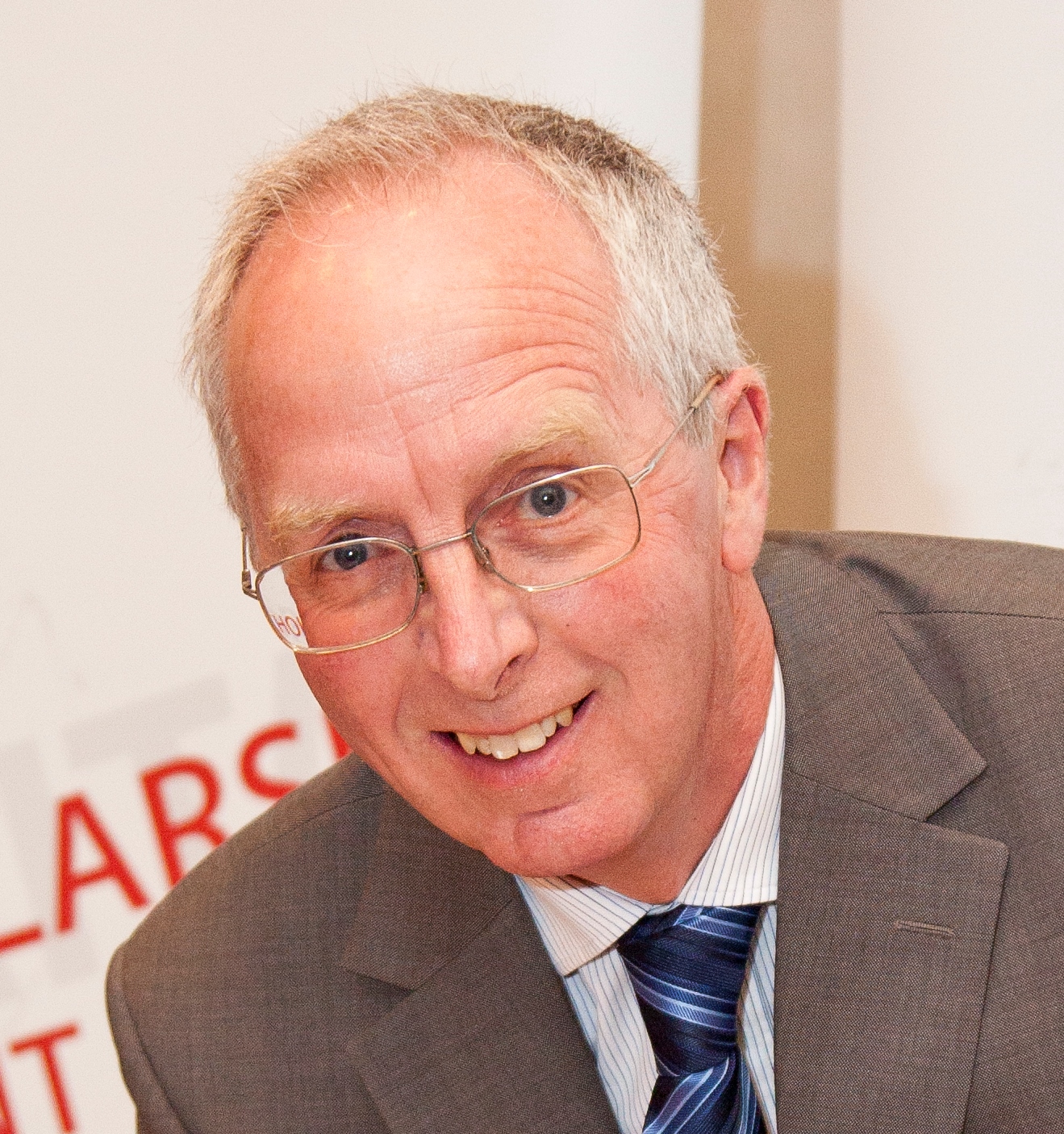
The USACE has well established hydraulic hydrologic tools for simulating Newtonian flows but the tools available for non-Newtonian flows are quite limited. A wide range natural flows present non-Newtonian properties including mudflows, debris flows, lahars, and snow avalanches. Non-Newtonian fluids have a shear rate vs shear stress relationship which can be nonlinear and/or does not pass though the origin. The accuracy of standard flow measurement technologies is hindered by the non-Newtonian fluid properties.In Newtonian fluids the relationship between shear rate and shear stress is linear and passes though the origin. Testing of DEF efficacy and usage often requires accurate measurement of flow over set time periods. This liquid is poured into many diesel truck engines to reduce emissions by breaking down soot and unburnt fuel into nitrogen and water byproducts. Diesel exhaust fluid (DEF) is a non-Newtonian fluid solution mixture of 32.5% urea and 67.5% DI water. Less viscous non-Newtonian fluids, such as polymer solutions, are perfect for use with Coriolis instruments like Alicat’s CODA-Series mass flow meters and controllers. Some non-Newtonian fluids are highly viscous-for example, cement slurries, yogurt, and honey-and may not be compatible with certain Coriolis devices. While Coriolis instruments have been shown to be the most effective solution for flowing non-Newtonian fluids, it is still important to be aware of the technology’s limitations. This was validated by a University of Liverpool study that found Coriolis flow devices to operate within the specified accuracy tolerance when used with non-Newtonian fluids. These characteristics decrease the measurement accuracy of flow meters that rely on expected flow velocity profiles.Ĭoriolis mass flow instruments are able to accurately measure and control non-Newtonian fluid flow rates due to their unique operating principle which uses inertial forces to directly determine mass flow rates. Non-Newtonian fluids have different velocity profiles compared to Newtonian fluids, and also behave differently when transitioning between laminar and turbulent flows. When selecting a flow meter or controller, it is critical to consider the behavior of fluids used in the process. Flowing non-Newtonian fluids using Coriolis technology Changing parameters such as pipe diameter, flow rate, and pressure all have an effect on the magnitude of shear stress present, and thus also on the fluid’s viscosity and velocity profile. Process conditions can introduce further variability to a non-Newtonian fluid’s behavior. Effect of shear stress on non-Newtonian fluids (thixotropic & rheopectic) What other conditions affect non-Newtonian fluids? The resulting velocity profile is then predictable as a function of the shear stress.įigure 2b. This leads to a faster fluid flow at the center of the pipe, and a slower fluid flow at the pipe walls. In the diagram below, you can see that when Newtonian fluids flow through a pipe, increased shear stress near the pipe walls causes a decrease in velocity. For Newtonian fluids, these shear forces do not lead to a change in viscosity, and the flows have predictable velocity profiles. Newtonian fluidsįor any process fluid moving through a pipe, shear forces are caused by the molecules inside the fluid moving past each other. Non-Newtonian fluids, on the other hand, change in viscosity depending on the type and magnitude of forces exerted upon them. Newtonian fluids-for example, water-exhibit a constant viscosity regardless of any applied force.
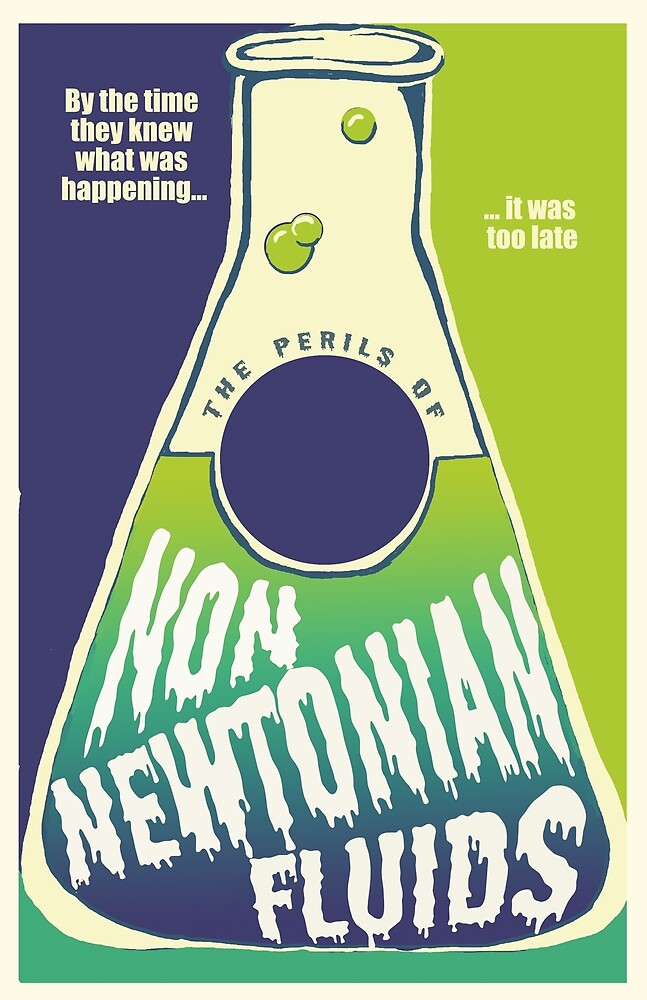
In this blog, we will discuss the challenges posed by non-Newtonian fluids and how Coriolis flow instruments have proven to be the most successful solution. Ultrasonic flow meters have also shown up to 15% deviation when used for non-Newtonian fluids transitioning between laminar and turbulent flow. Some popular flow technologies like electromagnetic meters can exhibit up to a 20% deviation in accuracy when used for such fluids. Finding the right instrument to measure or control non-Newtonian fluids can be a challenge.
